With the smallest footprint in the industry, the SWR-TIPTIG is a cobot designed specifically for pipe, pressure vessel, and roll welding applications using the Gas Tungsten Arc Welding (GTAW or TIG) process. This system pushes the limits of TIG welding to new heights using the advanced TIPTIG system, enhancing both speed and precision far beyond conventional standards. The SWR-TIPTIG not only significantly boosts productivity but also distinctly sets your operations above the competition in a demanding market.
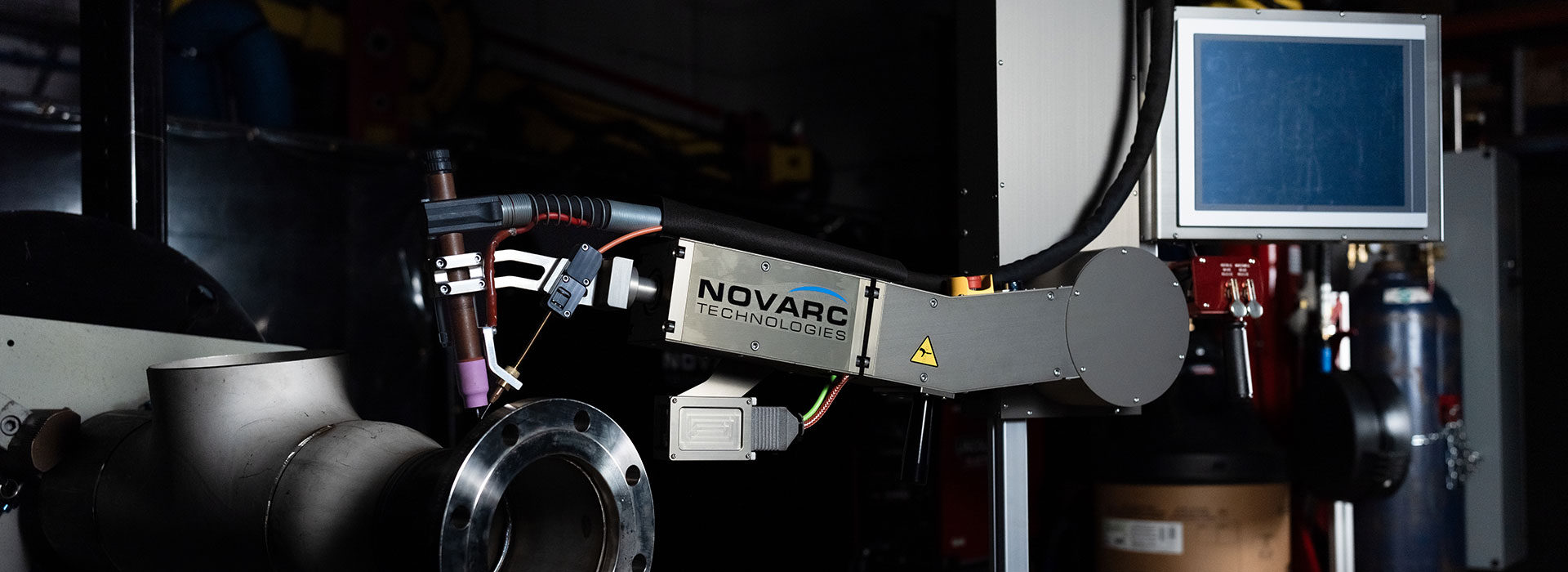
Spool Welding Robot (SWR™)
TIPTIG
Lead the industry, secure more bids, and speed through projects.
What is SWR-TIPTIG?
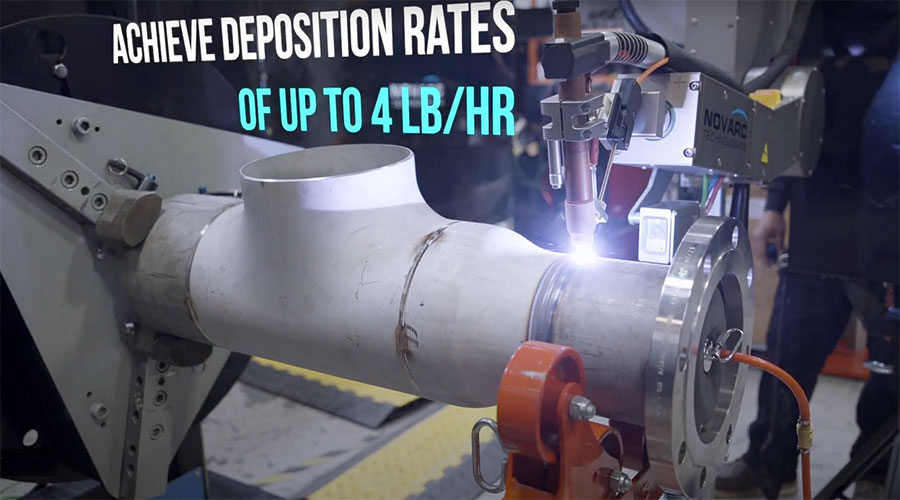
The SWR-TIPTIG Difference
Increased Welding Speed and Quality
Up to 60% Cost Savings
TIP TIG Hot Wire TIG System Integration
Versatile Material Compatibility
*With the purchase of NovCare Gold
[2] Arc-on time only, excluding interpass cooling time
The Future at Your Fingertips
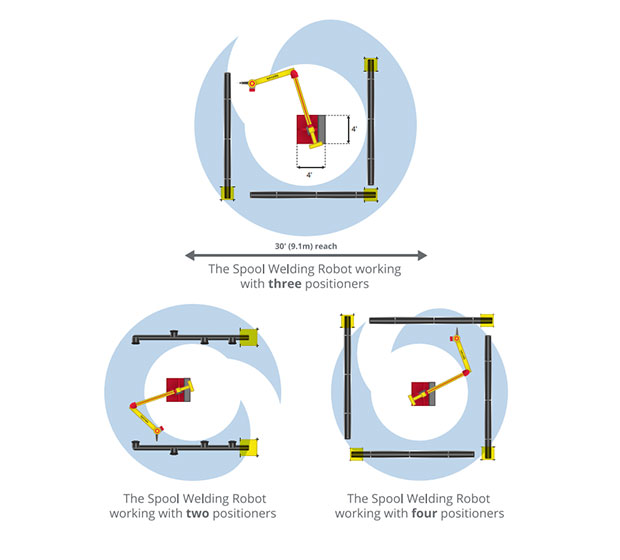
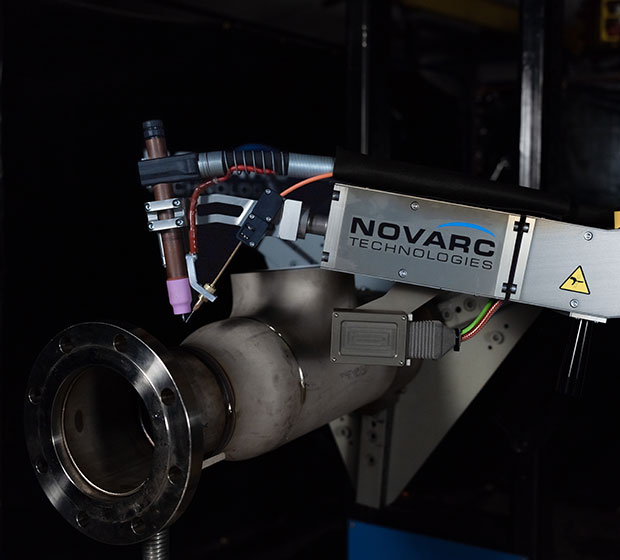
Smallest Industry Footprint
Collaborative TIG Welding Solution
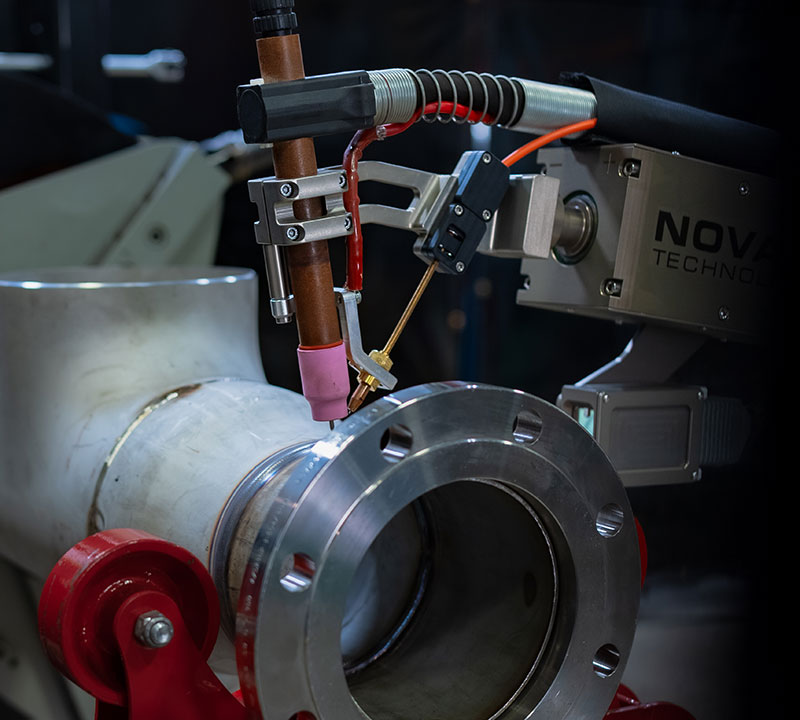
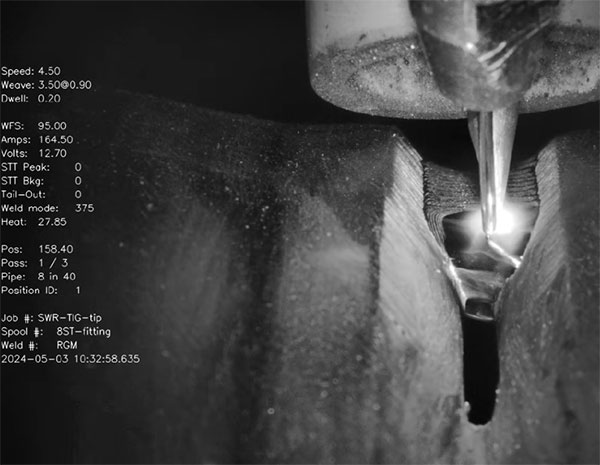
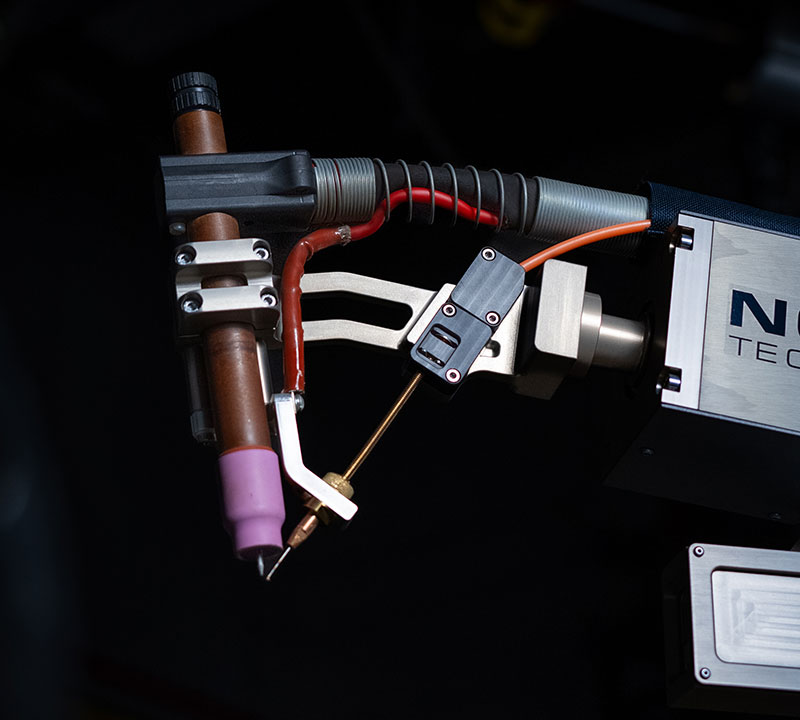
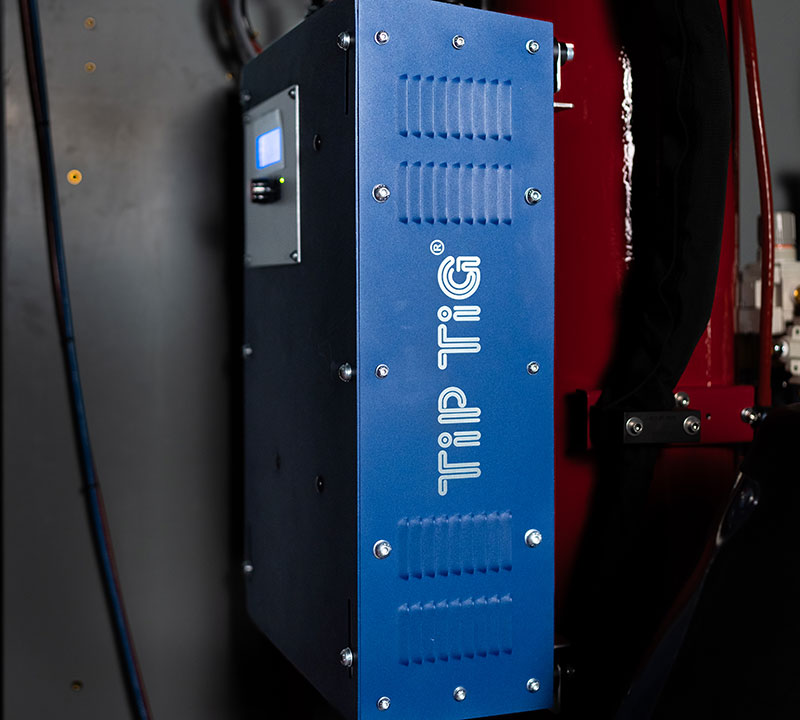
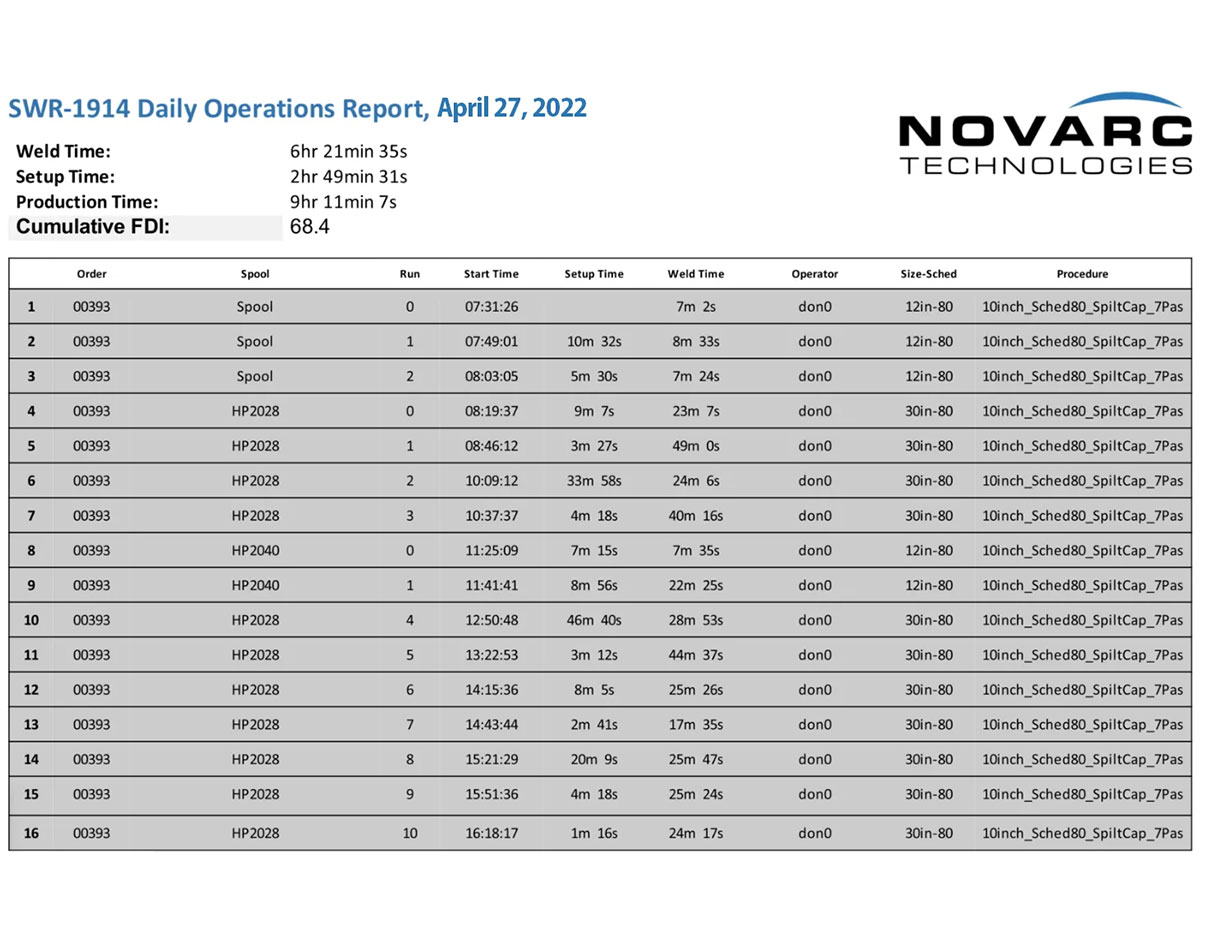
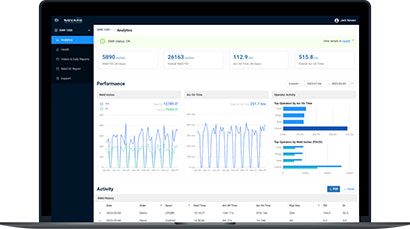
Up to 300% Increase in Travel Speeds
Cutting edge weld imaging system
Witness the future of weld monitoring with our advanced imaging system. Real-time clarity gives SWR-TIPTIG operators unprecedented visibility into the welding process, ensuring unmatched precision and accuracy in every weld.
- Enhanced view of the groove, puddle, and stick
- Every weld is recorded in real-time with key weld parameters embedded on the screen
- Improve weld quality by analyzing recorded videos in parallel with the weld parameters saved by NovData™
Hot Filler Wire Technology
Patented TipTIG Feeding System
The SWR-TIPTIG System incorporates TipTIG, utilizing a patented feeding system. This system superimposes feeding in parallel through a backward/forward movement. This innovative design breaks the surface tension of the puddle, leading to improved solidification of the weld pool and ensuring impeccable weld quality.
- Track and Improve your pipe welding productivity with the automatically generated daily operations reports
- Bid competitively on projects by applying cost savings gathered from daily operations reports
- Manage and track the critical weld parameters for accurate troubleshooting and enhanced quality control practices with the log reports automatically generated for each weld
NovData™
Novarc’s comprehensive production monitoring software, NovData™, improves traceability into your production by automatically creating in-depth production reports.
Here are some highlights of NovData™
- Track and Improve your pipe welding productivity with the daily operations reports automatically generated every day
- Bid competitively on projects by applying cost savings gathered from daily operations reports
- Manage and track the critical weld parameters for accurate troubleshooting and enhanced quality control practices with the log reports automatically generated for each weld
NovSync™
The NovSync™ dashboard helps you to track production and machine trends over time by giving you centralized and secure access to weld videos, daily reports, and NovData™ logs.
You can now get remote, easy access to actionable insights needed to improve your welding operations and become more competitive in your market.
Novarc Technologies
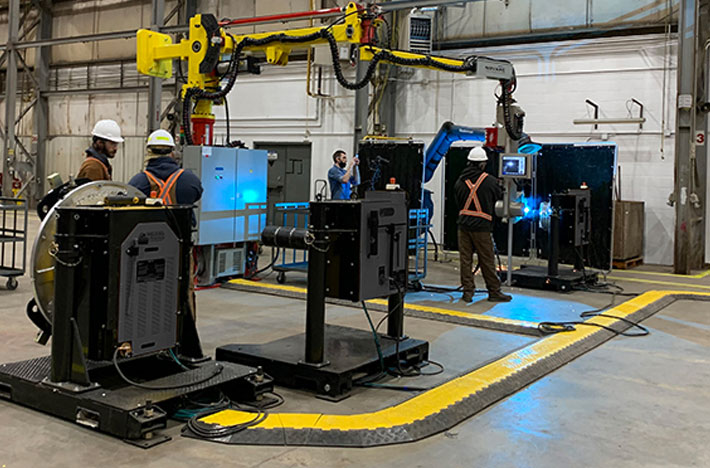
Positioner Integration
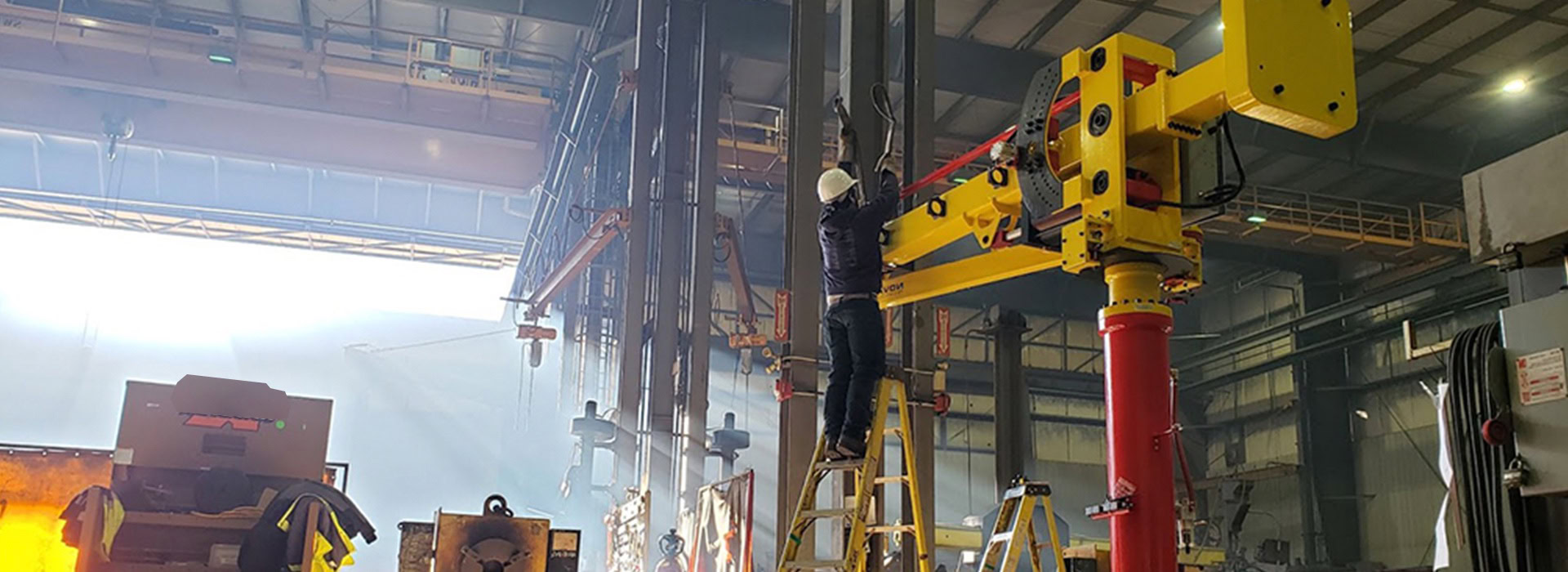
NovCare Service and Support Packages
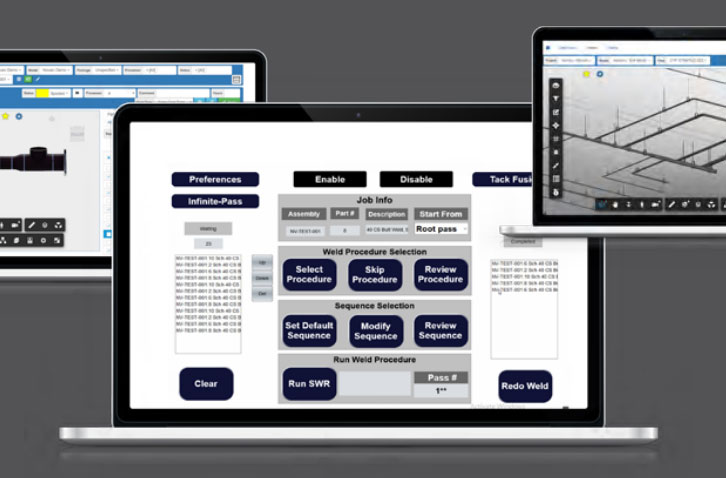
BIM Software Integration
SWR™ TIPTIG Technical Specifications
Applications
Pipe and pressure vessels from 2”- 16” (5cm – 40cm)*Height
15 ft (4.5m)Materials
Carbon and low alloy steels, Stainless and nickel alloys*SWR Footprint
4’x4’ (1.2m x 1.2m)Weld Processes
GTAWWeight
Approximately 3500 lb.Wire Diameter
0.035 in. (0.9 mm)Reach
15 ft (4.5m)Power Requirements
SWR™ Requirements
North America – 3-Phase, 208Y/120V, 60Hz, 23A, 5 Wires (V, U, W, Neutral and Ground)EU and AUS – 3 Phase, 400/208/120VAC, 60 A, 50/60 Hz
Lincoln Electric Power Source Requirements
North America – 3-Phase AC Voltage/Current: 208V/60A, 230V/54A, 400V/31A, 460V/27A, 575V/21A, 4 Wires (V, U, W and Ground)EU and AUS – distributed from SWR electrical cabinet